
Новая керамическая смесь для 3D-печати твердеет мгновенно
По мнению китайских учёных из Университета Цзяннань, будущее напечатанных изделий зависит от керамической суспензии. Под руководством профессора Лю Жэня они разработали технологию, которая позволяет создавать сложные формы, ранее невозможные при традиционной 3D-печати. Они добились этого, создав керамическую смесь, которая практически мгновенно затвердевает под воздействием инфракрасного света.
Преимущества известных технологий 3D-печати нередко тускнеют из-за проблем с точностью, скоростью и экономичностью. Например, при методе стереолитографии используют лазерные лучи, чтобы сплавить воедино мелкие частицы сырья: пластика, металла, стекла или керамического порошка. Чтобы получился качественный твёрдый объект, для крупномасштабных или причудливой формы конструкций обычно требуются также некие подпорки до затвердевания компонентов. А это увеличивает время и стоимость крупных проектов.
А затем эти «костыли» в стереолитографии ещё предстоит удалить, что создаёт проблемы с точностью размеров и гладкостью поверхности. Кроме того, удаление подпорок может привести к появлению микротрещин и даже к разрушению напечатанных изделий.
Альтернативные процессы производства 3D-керамики позволили печатать фигурки без вспомогательных конструкций, используя ультрафиолетовое излучение для затвердевая компонентов. Такие методы стали прогрессом. Но и тогда возникло препятствие — ультрафиолетовое излучение не могло проникать внутрь керамического материала. Учёные Цзяннаньского университета нашли обходной путь. Они обнаружили, что могут создавать объекты быстрее и с большей прочностью, используя керамическую пасту, которая твердеет под инфракрасным излучением.
Изобретатели заявили в журнале Nature Communications, что их керамическую суспензию можно делать твёрдой на месте во время 3D-печати без дополнительных конструкций. При этом повышенная прочность и способность к самоподдержке повышает точность изготовления. Что ещё более важно, метод облегчает печать даже горизонтальных выступов без провисания или наклона, то есть без дефектов.
При тестировании получалось создавать сложные объекты, которые были достаточно прочными, чтобы сохранять свою форму и стабильность сразу после выхода материала из принтера.
Когда инженеры протестировали глубину отверждения суспензии, то обнаружили, что под традиционным ультрафиолетовым излучением глубина отверждения достигла 1,02 мм чуть более чем за две минуты. Но при использовании ближнего инфракрасного излучения глубина отверждения была в три раза выше, а время до необходимой прочности — всего 3 секунды.
Подводя итог своим результатам, учёные заявили, что их технология позволяет получать объекты с более высоким разрешением и уникальным внешним видом.
Преимущества известных технологий 3D-печати нередко тускнеют из-за проблем с точностью, скоростью и экономичностью. Например, при методе стереолитографии используют лазерные лучи, чтобы сплавить воедино мелкие частицы сырья: пластика, металла, стекла или керамического порошка. Чтобы получился качественный твёрдый объект, для крупномасштабных или причудливой формы конструкций обычно требуются также некие подпорки до затвердевания компонентов. А это увеличивает время и стоимость крупных проектов.
А затем эти «костыли» в стереолитографии ещё предстоит удалить, что создаёт проблемы с точностью размеров и гладкостью поверхности. Кроме того, удаление подпорок может привести к появлению микротрещин и даже к разрушению напечатанных изделий.
Альтернативные процессы производства 3D-керамики позволили печатать фигурки без вспомогательных конструкций, используя ультрафиолетовое излучение для затвердевая компонентов. Такие методы стали прогрессом. Но и тогда возникло препятствие — ультрафиолетовое излучение не могло проникать внутрь керамического материала. Учёные Цзяннаньского университета нашли обходной путь. Они обнаружили, что могут создавать объекты быстрее и с большей прочностью, используя керамическую пасту, которая твердеет под инфракрасным излучением.
Изобретатели заявили в журнале Nature Communications, что их керамическую суспензию можно делать твёрдой на месте во время 3D-печати без дополнительных конструкций. При этом повышенная прочность и способность к самоподдержке повышает точность изготовления. Что ещё более важно, метод облегчает печать даже горизонтальных выступов без провисания или наклона, то есть без дефектов.
При тестировании получалось создавать сложные объекты, которые были достаточно прочными, чтобы сохранять свою форму и стабильность сразу после выхода материала из принтера.
Когда инженеры протестировали глубину отверждения суспензии, то обнаружили, что под традиционным ультрафиолетовым излучением глубина отверждения достигла 1,02 мм чуть более чем за две минуты. Но при использовании ближнего инфракрасного излучения глубина отверждения была в три раза выше, а время до необходимой прочности — всего 3 секунды.
Подводя итог своим результатам, учёные заявили, что их технология позволяет получать объекты с более высоким разрешением и уникальным внешним видом.
- Дмитрий Ладыгин
- pixabay.com
Наши новостные каналы
Подписывайтесь и будьте в курсе свежих новостей и важнейших событиях дня.
Рекомендуем для вас
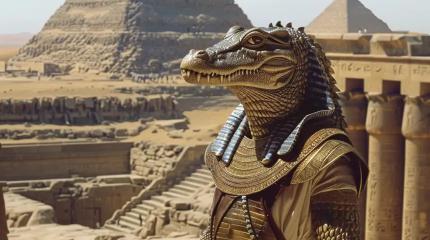
Вот уже 17 лет власти Египта запрещают археологам исследовать легендарный Лабиринт
Что скрывает Египет: библиотеку Атлантиды или доказательства переписывания истории?...
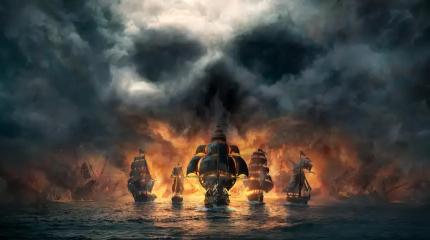
Тайна пиратского корабля за 138 миллионов долларов раскрыта у берегов Мадагаскара
Шторм, предательство, тонны золота: Как капитан Стервятник похитил сокровища португальской короны....
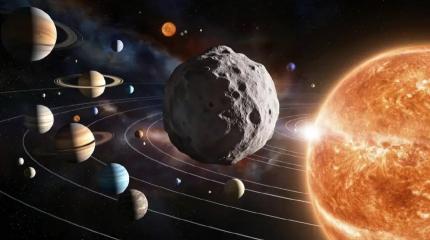
Третий гость из бездны: NASA официально подтвердило межзвездное происхождение объекта 3I/ATLAS
Скорость в 245 000 км/ч! Астрофизики говорят, гость «прострелит» Солнечную систему как пуля....
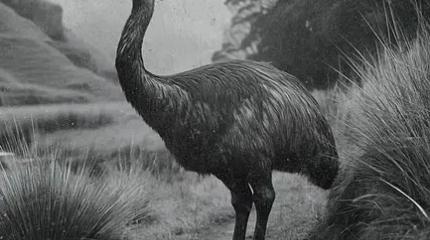
Воскрешение монстра: Colossal возвращает к жизни 3,6-метровую птицу-убийцу моа!
Сможет ли 230-килограммовый гигант из Новой Зеландии выжить среди людей?...
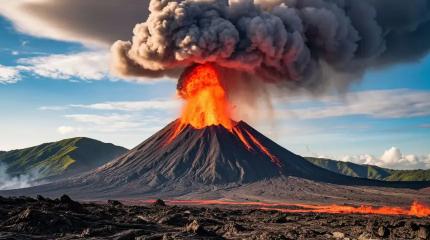
Эксперты бьют тревогу: Таяние ледников разбудит вулканы по всему миру
Цепная реакция извержений прокатится от Антарктиды до Камчатки. Выбросы пепла и CO2 сделают климат невыносимым....
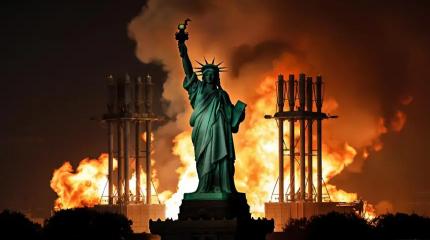
«Богатые тоже плачут»: США открыли «новую эру энергетики» — 800 часов в год без света!
Штаты хвастались ИИ, а электросети «горят» даже от чат-ботов… Россия тем временем запускает термояд....
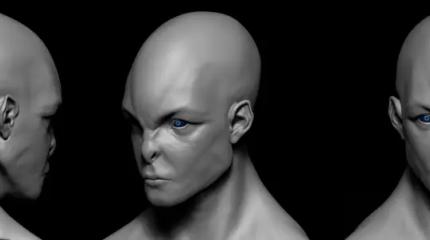
Череп ребенка-«пришельца» из Аргентины оказался вполне земным
Эксперты рассказали в подробностях, как могла появиться «инопланетная» форма головы....